Joining Technologies | 11/27/2024 | 4 Min Read:
Wire EDM (Electrical Discharge Machining) is a marvel of modern manufacturing, known for its precision and versatility. Used widely in industries like aerospace, automotive, and medical device manufacturing, this non-conventional machining process has revolutionized how intricate and high-tolerance components are produced.
In this blog post, we’ll delve into what Wire EDM is, how it works, its applications, and advantages.
What is Wire EDM?
Wire EDM is a subtractive manufacturing process that uses electrical discharges (sparks) to cut conductive materials. A thin wire, often made of brass or copper, serves as the electrode. Unlike traditional cutting methods that rely on physical force, it erodes material through electrical energy, achieving unmatched precision.
The process is ideal for cutting hard metals like titanium, tungsten, and stainless steel, as well as creating intricate shapes and designs in softer conductive materials.
How Does It Work?
Setup – A workpiece is submerged in a dielectric fluid, typically deionized water, which helps to control the spark discharges and cools the cutting area.
Wire Movement – A spool-fed wire is stretched between guides and moves in a controlled path dictated by CNC (Computer Numerical Control) programming.
Spark Erosion – As the wire comes close to the workpiece, electrical pulses create sparks that erode the material. The wire itself does not come into physical contact with the material
Precision Control – The dielectric fluid flushes away debris, ensuring clean cuts and preventing shorts between the wire and the material.
This process can achieve tolerances as tight as ±0.002 inches, making it a preferred choice for demanding applications.
What Are Some Applications?
Wire EDM is celebrated for its ability to handle complex geometries and tight tolerances. Common applications include:
Medical Devices: Production of surgical instruments and implants that demand high precision.
Aerospace Components: Crafting turbine blades, fuel injectors, and other intricate parts.
Molds and Dies: Creating intricate molds for plastics and metals.
Micro-Machining: Producing tiny, detailed parts for electronics and micromechanical systems.
Advantages of Wire EDM?
High Precision – This process is renowned for creating parts with exceptional accuracy and smooth finishes.
Material Versatility – It can cut any conductive material, regardless of hardness.
No Mechanical Stress – The non-contact nature eliminates stress on the material, preventing distortion.
Complex Cuts – Ideal for intricate shapes, tight corners, and fine details.
Minimal Waste – The precise nature of the process reduces material waste.
Wire EDM machining is a cornerstone of precision engineering, offering unparalleled accuracy and flexibility for complex manufacturing needs. Whether you’re crafting aerospace components or intricate medical devices, Wire EDM delivers results that are difficult to achieve with other machining methods.
Request a Quote Today!
At Joining Technologies, you can take advantage of our Wire EDM as a standalone offering or in conjunction with our machining services and build-to-print services. Click here to request a quote now.
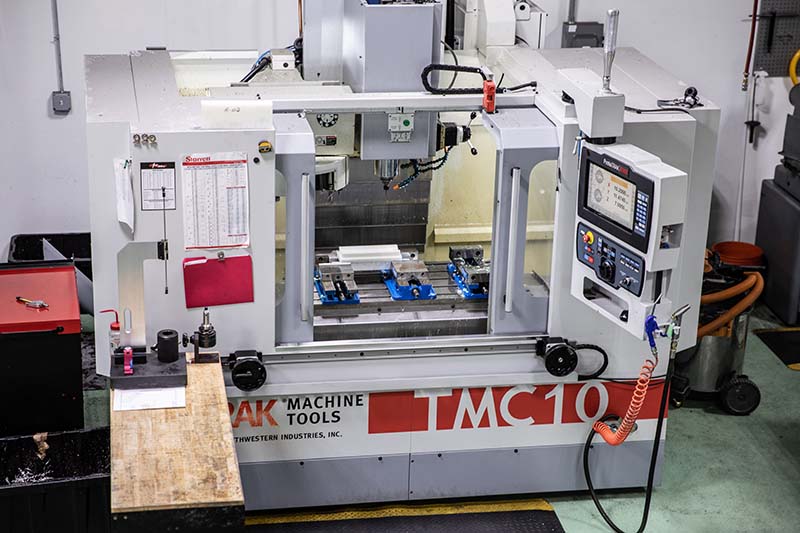
Have Some Questions?
Let us answer them by clicking the button below!