Joining Technologies | 2/27/2025 | 4 Min Read:
Copper is one of the most versatile and sought-after metals in the manufacturing world. Its excellent electrical and thermal conductivity makes it a popular material across industries. This includes electronics, automotive, aerospace, and renewable energy. However, welding this metal has always been a challenging task.
Why is Copper Welding a Pain?
This is due to its high thermal conductivity and reflectivity. Enter laser welding, a game-changing solution that has revolutionized this process. In this blog, we’ll dive into why this is a preferred method for this material’s welding applications and how it benefits modern manufacturing.
Challenges of Copper Welding
Welding copper presents unique challenges:
High Thermal Conductivity – Copper dissipates heat rapidly, making it difficult to achieve the required heat concentration for a strong weld.
Reflectivity – Copper reflects a significant amount of laser energy, especially in the infrared spectrum, leading to inefficiencies in traditional welding methods.
Oxidation – Copper tends to oxidize during welding, potentially weakening the weld joint.
These challenges demand precision, control, and advanced technology—qualities that laser welding provides.
Why Laser Welding for Copper?
Laser welding has emerged as a leading solution due to its precision, speed, and adaptability. Here’s why it’s an ideal choice:
Localized Heat Input:
Laser welding delivers highly concentrated energy to a small area, minimizing heat dissipation and ensuring efficient melting of the copper material. This localized heat input reduces the risk of distortion and thermal damage to surrounding components.
Overcoming Reflectivity:
Modern laser welding systems utilize high-power lasers (such as green or blue wavelength lasers) that are better absorbed by copper. This ensures reliable energy transfer and consistent welding results.
High-Speed Precision:
Laser welding allows for fast and precise welding of intricate designs, making it ideal for applications such as microelectronics, battery assembly, and thin copper components.
Minimal Oxidation:
With options to perform welding in controlled atmospheres, laser welding minimizes oxidation during the process, resulting in cleaner, stronger welds.
Adaptability:
Laser welding is versatile and compatible with various joint geometries and thicknesses, from micro-welding applications to thicker copper sheets.
Applications of Laser Welding Copper
The use of this process on copper material has seen significant growth in several key industries:
Electronics –Joining copper components for circuit boards, connectors, and microchips with extreme precision.
Automotive – Welding copper in electric vehicle batteries and motor components.
Aerospace – Ensuring reliable connections in high-performance systems.
Renewable Energy – Solutions for solar panel assemblies and wind turbines.
The Joining Technologies Advantage
At Joining Technologies, we harness cutting-edge welding systems to tackle the challenges of this material with precision and expertise. Our approach focuses on:
- Delivering exceptional weld strength and quality
- Customizing solutions to match the unique requirements of your projects
- Utilizing advanced technology and industry-leading processes to ensure superior results
Whether you’re working on next-generation electronics or renewable energy components, our team is ready to bring unparalleled precision and quality to your needs.
Partner with Us For Your Projects!
Copper is the backbone of many modern innovations, and with laser welding, the possibilities for using copper in advanced applications are virtually limitless. If you’re ready to take your copper welding projects to the next level, Joining Technologies is here to help.
Contact us today to learn more about how our laser welding solutions can enhance your manufacturing processes.
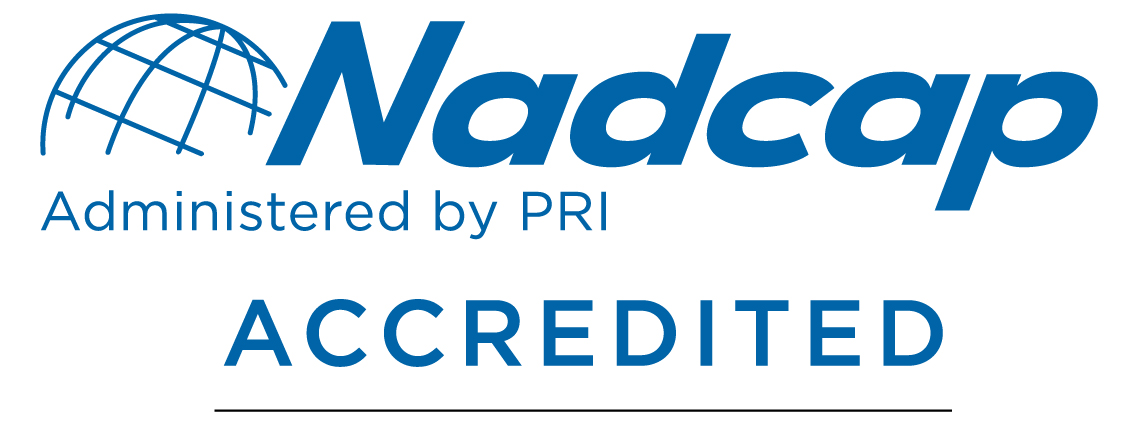
Have Some Questions?
Let us answer them by clicking the button below!