Copper Welding and the Advantages with Laser Technology
Joining Technologies | 2/27/2025 | 4 Min Read:
Copper is one of the most versatile and sought-after metals in the manufacturing world. Its excellent electrical and thermal conductivity makes it a popular material across industries. This includes electronics, automotive, aerospace, and renewable energy. However, welding this metal has always been a challenging task.
Why is Copper Welding a Pain?
This is due to its high thermal conductivity and reflectivity. Enter laser welding, a game-changing solution that has revolutionized this process. In this blog, we’ll dive into why this is a preferred method for this material’s welding applications and how it benefits modern manufacturing.
Challenges of Copper Welding
Welding copper presents unique challenges:
High Thermal Conductivity – Copper dissipates heat rapidly, making it difficult to achieve the required heat concentration for a strong weld.
Reflectivity – Copper reflects a significant amount of laser energy, especially in the infrared spectrum, leading to inefficiencies in traditional welding methods.
Oxidation – Copper tends to oxidize during welding, potentially weakening the weld joint.
These challenges demand precision, control, and advanced technology—qualities that laser welding provides.
Why Laser Welding for Copper?
Laser welding has emerged as a leading solution due to its precision, speed, and adaptability. Here’s why it’s an ideal choice:
Localized Heat Input:
Laser welding delivers highly concentrated energy to a small area, minimizing heat dissipation and ensuring efficient melting of the copper material. This localized heat input reduces the risk of distortion and thermal damage to surrounding components.
Overcoming Reflectivity:
Modern laser welding systems utilize high-power lasers (such as green or blue wavelength lasers) that are better absorbed by copper. This ensures reliable energy transfer and consistent welding results.
High-Speed Precision:
Laser welding allows for fast and precise welding of intricate designs, making it ideal for applications such as microelectronics, battery assembly, and thin copper components.
Minimal Oxidation:
With options to perform welding in controlled atmospheres, laser welding minimizes oxidation during the process, resulting in cleaner, stronger welds.
Adaptability:
Laser welding is versatile and compatible with various joint geometries and thicknesses, from micro-welding applications to thicker copper sheets.
Applications of Laser Welding Copper
The use of this process on copper material has seen significant growth in several key industries:
Electronics –Joining copper components for circuit boards, connectors, and microchips with extreme precision.
Automotive – Welding copper in electric vehicle batteries and motor components.
Aerospace – Ensuring reliable connections in high-performance systems.
Renewable Energy – Solutions for solar panel assemblies and wind turbines.
The Joining Technologies Advantage
At Joining Technologies, we harness cutting-edge welding systems to tackle the challenges of this material with precision and expertise. Our approach focuses on:
- Delivering exceptional weld strength and quality
- Customizing solutions to match the unique requirements of your projects
- Utilizing advanced technology and industry-leading processes to ensure superior results
Whether you’re working on next-generation electronics or renewable energy components, our team is ready to bring unparalleled precision and quality to your needs.
Partner with Us For Your Projects!
Copper is the backbone of many modern innovations, and with laser welding, the possibilities for using copper in advanced applications are virtually limitless. If you’re ready to take your copper welding projects to the next level, Joining Technologies is here to help.
Contact us today to learn more about how our laser welding solutions can enhance your manufacturing processes.
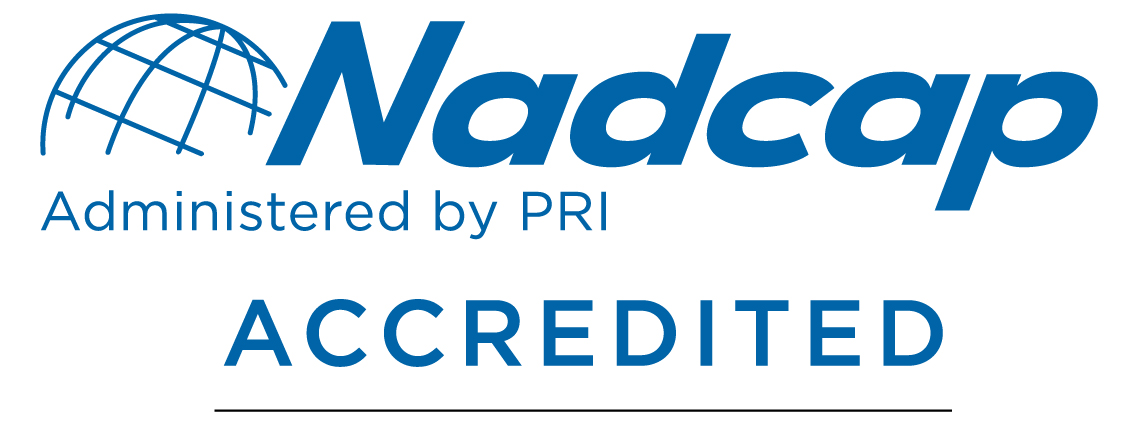
Have Some Questions?
Let us answer them by clicking the button below!
Achieving Excellence with NADCAP Accredited Welding
Joining Technologies | 2/5/2025 | 5 Min Read:
At Joining Technologies, we’re committed to delivering the highest quality welding services to our clients. As part of this commitment, we are proud to hold NADCAP accreditation for welding. But what exactly does this accreditation mean, and why is it important for your projects? Let’s explore.
What is NADCAP?
NADCAP, which stands for the National Aerospace and Defense Contractors Accreditation Program, is a globally recognized certification that establishes rigorous standards for special processes, including welding. Managed by the Performance Review Institute (PRI), NADCAP ensures that companies meet or exceed stringent quality requirements, particularly for industries where precision and reliability are paramount, such as aerospace, defense, and medical manufacturing.
What Does NADCAP Accreditation Mean for Welding?
NADCAP accreditation is not just a certificate—it’s a testament to a company’s dedication to excellence. Here’s what it signifies for welding processes:
Stringent Quality Standards – Achieving NADCAP accreditation requires adherence to comprehensive quality requirements, from materials and procedures to equipment calibration and operator training.
Consistent Performance – Accredited companies must demonstrate repeatable and reliable welding processes through rigorous testing and documentation.
Industry Recognition – NADCAP is recognized worldwide as a mark of excellence, providing confidence to clients and partners that they are working with a trusted provider.
The Joining Technologies Advantage
At Joining Technologies, our NADCAP-accredited welding services set us apart from the competition. Here’s how our certification benefits your projects:
Uncompromising Quality – Every weld we perform meets the highest industry standards, ensuring safety, durability, and performance.
Advanced Techniques – Our team employs cutting-edge welding methods, including TIG, EBW, and laser welding, all validated under NADCAP’s rigorous criteria.
Skilled Team – Our certified welders undergo continuous training and assessments to maintain peak performance.
Aerospace and Beyond – While NADCAP is essential for aerospace applications, the precision and reliability it ensures are equally valuable in other industries such as defense, medical, and high-tech manufacturing.
Why NADCAP Matters for Your Projects
Choosing a NADCAP-accredited welding provider like Joining Technologies offers several key advantages!
Reliability – You can trust that our welding processes are proven and reliable, minimizing risks and ensuring compliance with stringent regulations.
Cost Savings – Accredited processes reduce the likelihood of defects and rework, saving time and money in the long run.
Global Confidence – With NADCAP accreditation, you can be assured that our services meet international quality benchmarks.
Partner with Joining Technologies!
When you work with Joining Technologies, you’re not just getting a service provider—you’re gaining a partner dedicated to excellence. Our NADCAP accreditation for welding is a reflection of our commitment to precision, quality, and innovation. Whether you’re in aerospace, defense, or any industry requiring impeccable welding standards, we’re here to help.
Contact us today to learn more about our accredited welding services and how we can support your next project.
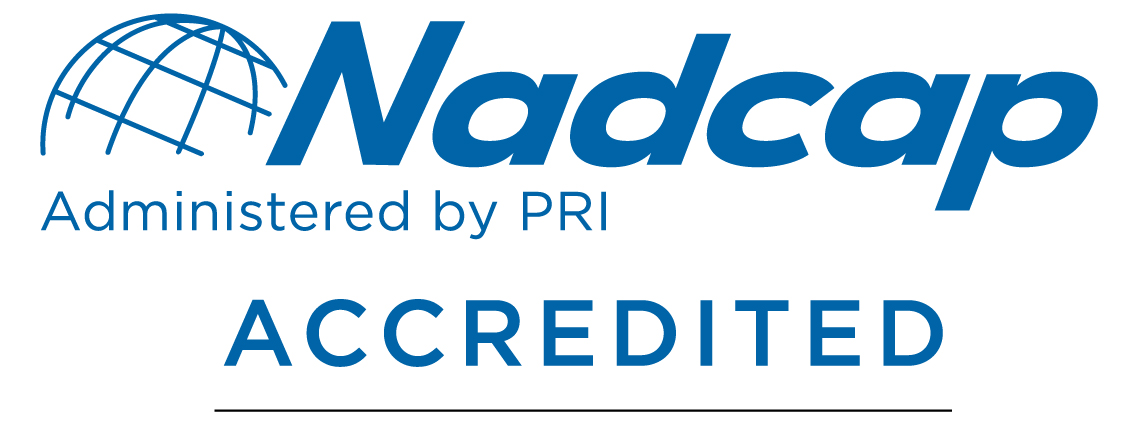
Have Some Questions?
Let us answer them by clicking the button below!
Wire EDM Machining Unveiled: Precision at Its Best
Joining Technologies | 11/27/2024 | 4 Min Read:
Wire EDM (Electrical Discharge Machining) is a marvel of modern manufacturing, known for its precision and versatility. Used widely in industries like aerospace, automotive, and medical device manufacturing, this non-conventional machining process has revolutionized how intricate and high-tolerance components are produced.
In this blog post, we’ll delve into what Wire EDM is, how it works, its applications, and advantages.
What is Wire EDM?
Wire EDM is a subtractive manufacturing process that uses electrical discharges (sparks) to cut conductive materials. A thin wire, often made of brass or copper, serves as the electrode. Unlike traditional cutting methods that rely on physical force, it erodes material through electrical energy, achieving unmatched precision.
The process is ideal for cutting hard metals like titanium, tungsten, and stainless steel, as well as creating intricate shapes and designs in softer conductive materials.
How Does It Work?
Setup – A workpiece is submerged in a dielectric fluid, typically deionized water, which helps to control the spark discharges and cools the cutting area.
Wire Movement – A spool-fed wire is stretched between guides and moves in a controlled path dictated by CNC (Computer Numerical Control) programming.
Spark Erosion – As the wire comes close to the workpiece, electrical pulses create sparks that erode the material. The wire itself does not come into physical contact with the material
Precision Control – The dielectric fluid flushes away debris, ensuring clean cuts and preventing shorts between the wire and the material.
This process can achieve tolerances as tight as ±0.002 inches, making it a preferred choice for demanding applications.
What Are Some Applications?
Wire EDM is celebrated for its ability to handle complex geometries and tight tolerances. Common applications include:
Medical Devices: Production of surgical instruments and implants that demand high precision.
Aerospace Components: Crafting turbine blades, fuel injectors, and other intricate parts.
Molds and Dies: Creating intricate molds for plastics and metals.
Micro-Machining: Producing tiny, detailed parts for electronics and micromechanical systems.
Advantages of Wire EDM?
High Precision – This process is renowned for creating parts with exceptional accuracy and smooth finishes.
Material Versatility – It can cut any conductive material, regardless of hardness.
No Mechanical Stress – The non-contact nature eliminates stress on the material, preventing distortion.
Complex Cuts – Ideal for intricate shapes, tight corners, and fine details.
Minimal Waste – The precise nature of the process reduces material waste.
Wire EDM machining is a cornerstone of precision engineering, offering unparalleled accuracy and flexibility for complex manufacturing needs. Whether you’re crafting aerospace components or intricate medical devices, Wire EDM delivers results that are difficult to achieve with other machining methods.
Request a Quote Today!
At Joining Technologies, you can take advantage of our Wire EDM as a standalone offering or in conjunction with our machining services and build-to-print services. Click here to request a quote now.
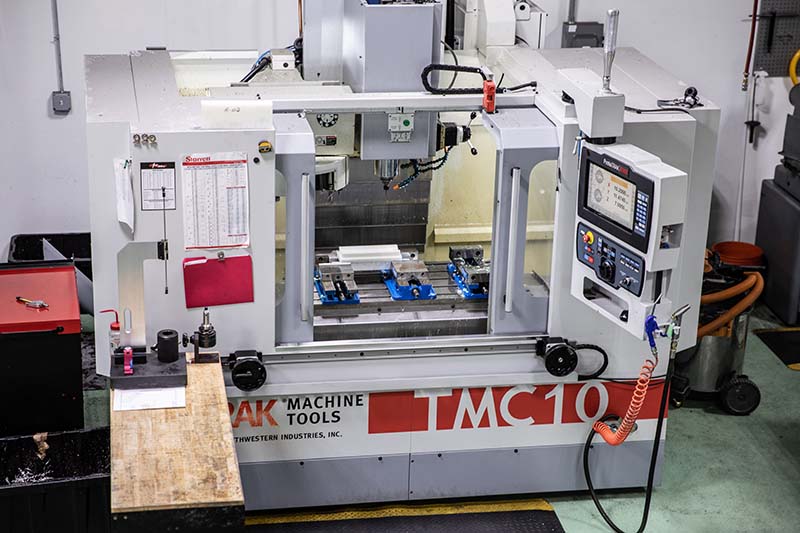
Have Some Questions?
Let us answer them by clicking the button below!
CNC Machining: A Guide To Revolutionizing Manufacturing
Joining Technologies | 10/25/2024 | 5 Min Read:
CNC machining, short for Computer Numerical Control machining, is one of the most transformative technologies in modern manufacturing. From aerospace components to custom jewelry, these machines play a vital role in producing precise and complex parts that would be difficult or impossible to make by hand. Whether you’re a manufacturing enthusiast, an engineer, or simply curious about technology, this post will give you a clear understanding of CNC machining, its key benefits, applications, and why it’s become an industry game-changer.
What is it exactly?
At its core, CNC machining is a manufacturing process where pre-programmed computer software dictates the movement of factory tools and machinery. CNC machines can be used to control a wide range of complex machinery, from grinders and lathes to mills and routers. These machines shape, cut, and drill materials with extreme precision based on the instructions of a CAD (computer-aided design) file.
Unlike traditional machining, where a skilled operator manually controls the tool, CNC machining automates the process. Once a part’s design is created and the program is loaded, the CNC machine takes over, guiding the tool to cut and shape the material with incredible accuracy.
So How Does It All Work?
CNC machining starts with the design phase, where engineers or designers create a digital model of the part or component using CAD software. This design is then converted into G-code, a programming language that CNC machines understand. G-code controls the speed, position, and path of the tools.
The material is secured onto the machine bed or fixture, and the tool (cutting, drilling, or milling) follows the G-code instructions to remove or add material as needed. The machine performs precise, repetitive operations, ensuring uniformity in production while drastically reducing human error.
Types of CNC Machines
CNC machining includes various types of machines, each specialized for different tasks. Here are the most common types:
CNC Milling Machines – These machines use rotating cutting tools to remove material from a workpiece. They can move along multiple axes (up to five or more) to create complex geometries.
CNC Lathes – In a CNC lathe, the workpiece rotates while a cutting tool removes material. This is ideal for creating cylindrical or symmetrical objects, such as shafts and gears.
CNC Routers – These machines are typically used for cutting softer materials like wood, plastic, or foam. CNC routers are widely used in woodworking and sign-making industries.
CNC Plasma Cutters – Plasma cutters use a plasma torch to cut through metals like steel, aluminum, or brass. These machines are known for cutting thick materials quickly.
CNC Electric Discharge Machines (EDM) – EDM machines use electrical discharges or sparks to remove material, primarily in hard metals that are difficult to machine with traditional methods.
Benefits of CNC Machining
CNC machining offers several advantages over manual machining or other traditional methods. Here’s why it’s so widely adopted:
High Precision – They follow programmed instructions with extreme accuracy, often achieving tolerances as small as a few microns. This level of precision is critical in industries like aerospace, medical devices, and automotive manufacturing.
Repeatability – Once a design is programmed, they can produce identical parts in large quantities with little to no variation. This makes it ideal for mass production.
Efficiency – They reduce the time required to produce complex parts. Since the machines can run 24/7 with minimal supervision, they significantly boost productivity.
Complex Geometries – Capabilities to create intricate and complex shapes that would be difficult to achieve through manual processes. Multi-axis CNC machines, in particular, can work on multiple faces of a part simultaneously.
Material Versatility – CNC machining works with a wide range of materials, including metals (aluminum, steel, titanium), plastics, wood, and foam. This flexibility makes it suitable for many industries.
Reduced Human Error – Since CNC machines are automated, there is less room for mistakes compared to manual operations. Human oversight is still needed for setup and maintenance, but the actual machining is highly reliable.
Scalability- Whether you need a single prototype or thousands of identical parts, CNC machining can easily scale to meet production needs.
Common Applications of CNC Machining
CNC machining is used across a variety of industries for its precision and adaptability. Some common applications include:
Aerospace – Precision components for engines, landing gear, and turbine blades are made using these machines due to their stringent tolerance requirements and complex designs.
Automotive – Produce parts such as gears, engine components, and custom modifications, where precision and performance are critical.
Medical Devices – Used to create surgical instruments, implants, and other medical devices that require exact dimensions and biocompatibility.
Electronics – It produces housings, enclosures, and other precise components for consumer electronics.
Prototyping – Designers and engineers rely on this for rapid prototyping, allowing them to test and iterate designs quickly.
Jewelry – Fine details and intricate designs required in jewelry making are easily achieved, offering both speed and accuracy.
Request a Quote Today!
At Joining Technologies, you can take advantage of our precision machining service as a standalone offering or in conjunction with our precision welding and build-to-print services. Click here to request a quote now.
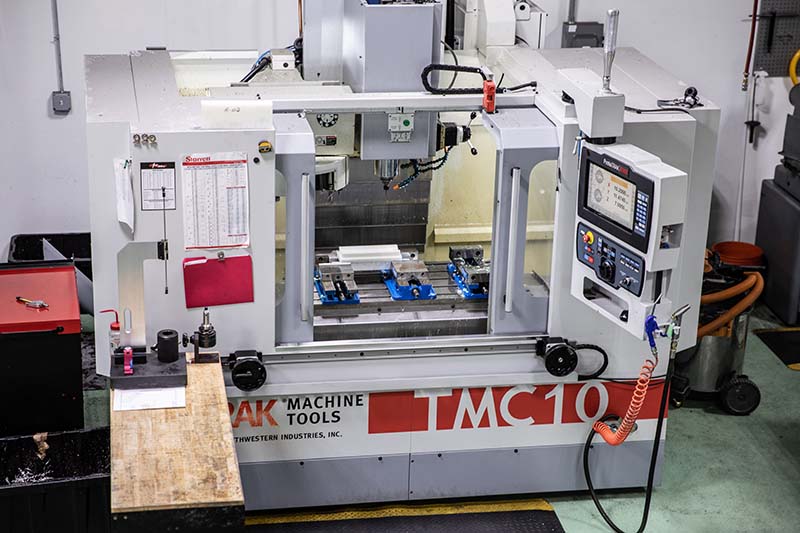
Have Some Questions?
Let us answer them by clicking the button below!
What is Hermetic Sealing and Why is it Important?
Joining Technologies | 9/27/2024 | 5 Min Read:
In today’s world, the need to protect sensitive components from external environments is more critical than ever. Whether you’re dealing with electronic devices, medical equipment, or aerospace systems, ensuring that no air, moisture, or contaminants can penetrate the enclosure is essential. This is where hermetic sealing comes into play.
Hermetic sealing is the process of making an object airtight to prevent the flow of gases, liquids, and other external elements into or out of the system. Derived from the Greek god Hermes, known for his ability to contain the elements, hermetic sealing has evolved to become a crucial component in numerous industries.
What Exactly is it?
Hermetic sealing creates an impermeable barrier, effectively protecting what’s inside from any external influence. A hermetic seal ensures that no gas, moisture, or contaminants can pass through, regardless of the surrounding conditions. This is achieved through precise engineering and materials, often using processes such as welding, brazing, or advanced adhesives.
The goal of hermetic sealing is to provide a lasting, airtight enclosure that can withstand extreme conditions—be it high pressure, temperature fluctuations, or exposure to corrosive elements.
How Does it Work?
To achieve an airtight seal, several methods and materials are used. Here are the most common ones:
-Welding
Welding is a highly reliable method for hermetic sealing, especially in industries like aerospace and medical devices. Techniques like TIG welding (GTAW) and laser welding ensure that metals fuse together to create an airtight bond. Welding is ideal for applications that require strength and long-term reliability.
-Brazing
Brazing is similar to welding but uses a filler metal that melts at a lower temperature than the base metals. This creates a strong bond without melting the core materials, often used in electronics and industrial applications where precision is essential.
-Glass-to-Metal Sealing
In some cases, especially in electronics, hermetic seals are created by bonding glass to metal. The differing thermal properties of glass and metal allow for an airtight seal when carefully heated and cooled. This method is common in the production of vacuum tubes, sensors, and medical equipment.
-Advanced Adhesives
For less extreme environments, adhesives can be used to form hermetic seals. These advanced adhesives are specially formulated to create impermeable barriers against moisture and gases, often used in consumer electronics and certain medical applications
The Importance of Hermetic Sealing
Hermetic sealing is essential in a wide range of industries, where protecting components from environmental exposure can be the difference between success and failure. Here are some of the most significant reasons why hermetic sealing is important:
-Preventing Contamination
In industries like pharmaceuticals, food packaging, and medical devices, contamination can have devastating effects. Hermetic sealing ensures that no contaminants such as dust, moisture, or microbes can enter the enclosure, maintaining sterility and preserving product integrity.
-Enhancing Durability
Hermetic seals protect components from environmental wear and tear, extending the lifespan of the products they enclose. In harsh environments, such as in the aerospace industry or underwater exploration, a hermetic seal ensures that sensitive systems can withstand extreme conditions.
-Ensuring Safety
In certain applications, a leak can be catastrophic. For example, in aerospace fuel systems, even a small breach in a seal could lead to dangerous leaks, risking the entire system. Hermetic seals ensure that gases and liquids stay contained, reducing the risk of accidents and ensuring the safety of both equipment and personnel.
-Improving Performance of Electronic Components
Electronic devices, especially those used in critical fields like telecommunications, aerospace, and military applications, rely on hermetic sealing to function properly. Exposure to humidity, air, or corrosive gases can degrade the performance of sensitive electronics. Hermetic enclosures keep these elements out, ensuring that circuits, sensors, and other components continue to operate reliably.
-Enabling Space Exploration
In space exploration, where equipment must endure the vacuum of space, drastic temperature swings, and cosmic radiation, hermetic sealing is non-negotiable. Every system aboard a spacecraft, from its fuel tanks to its communication devices, relies on airtight seals to function in these extreme environments.
Joining Tech Now Offering Hermetic Sealing
In conclusion, hermetic sealing is crucial for protecting sensitive components in industries ranging from aerospace to electronics. By ensuring airtight protection against environmental factors, it enhances durability, safety, and performance. At Joining Technologies, we offer advanced hermetic sealing solutions, primarily using laser welding to meet the demanding needs of our clients. Our expertise ensures that your systems remain secure and reliable, even in the most challenging environments.
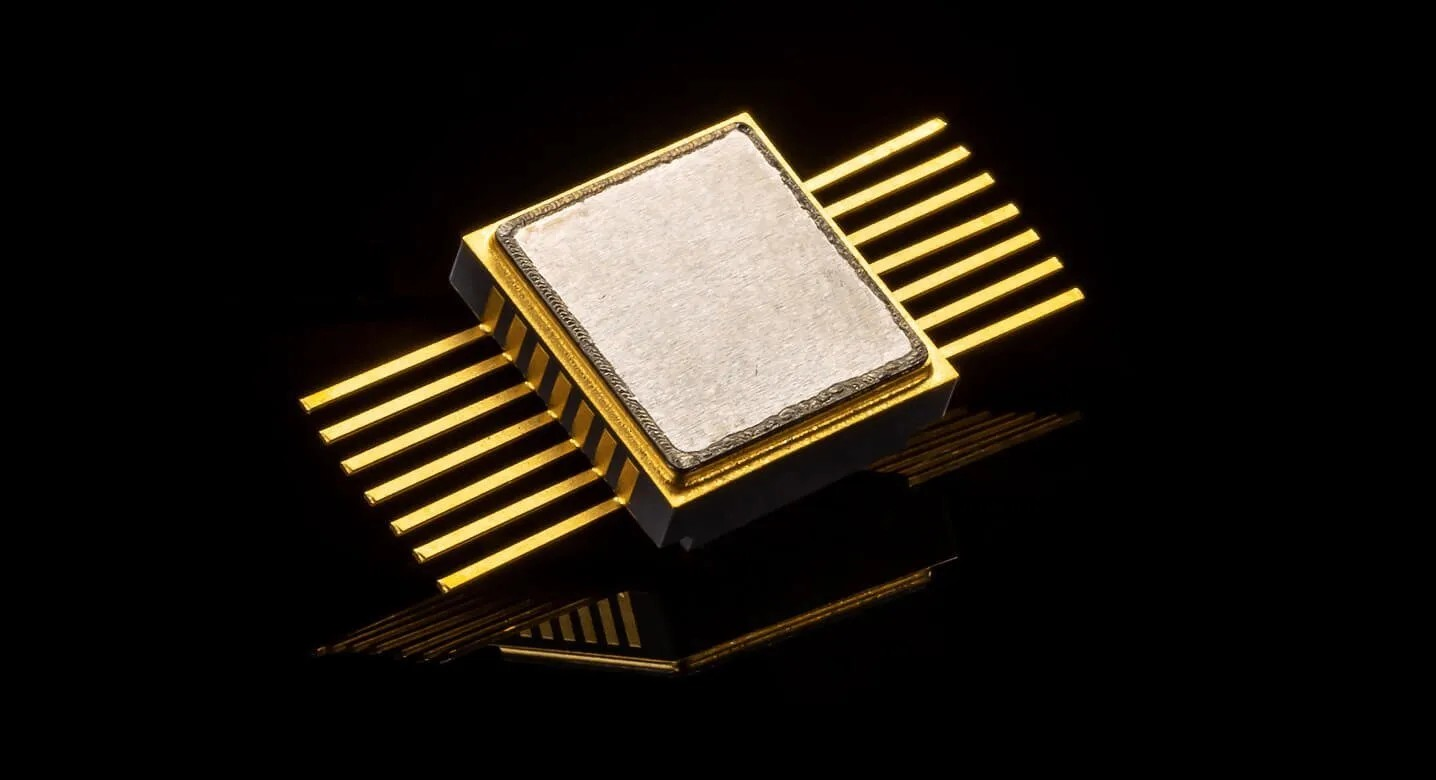
Have Some Questions?
Let us answer them by clicking the button below!
Joining Technologies, LLC Announces Increased EBW Capacity
2024 Update, New EBW Machine:
The Hartford Business Journal published an article in February 2023 highlighting the founding and 30-year evolution of what is now the Connecticut-based manufacturing powerhouse called Joining Industries. The article spoke of plans for continued growth in its subsidiaries, Joining Technologies in East Granby, and JT Automation in Windsor. Principals David Hudson and Michael Francoeur continue their growth plans as revealed in that article, with significant investment in modernization, equipment and people. Below is their latest EBW acquisition.
New Electron Beam Welding Capacity:
Joining Technologies installed a new electron beam welder in Q1 2024. The new equipment was purchased from Evobeam GmbH and brings a new game-changing capability with the latest technology package for managing automated weld parameters. Integrated metrology and seam tracking software ensure the highest level of weld repeatability without operator intervention. The super-fast vacuum cycle coupled with seam tracking and CNC motion will deliver high precision welds at a lower cost to our customers.
Electron beam welding (EBW) is typically used on critical, high value components in aerospace, nuclear and other industries requiring precise parameter management and repeatability. The process is well suited to applications with dissimilar metals, deep weld penetrations and oxidation-free process requirements. Joining Technologies maintains a variety of qualified electron beam welding equipment for a wide range of materials, and component size variations.
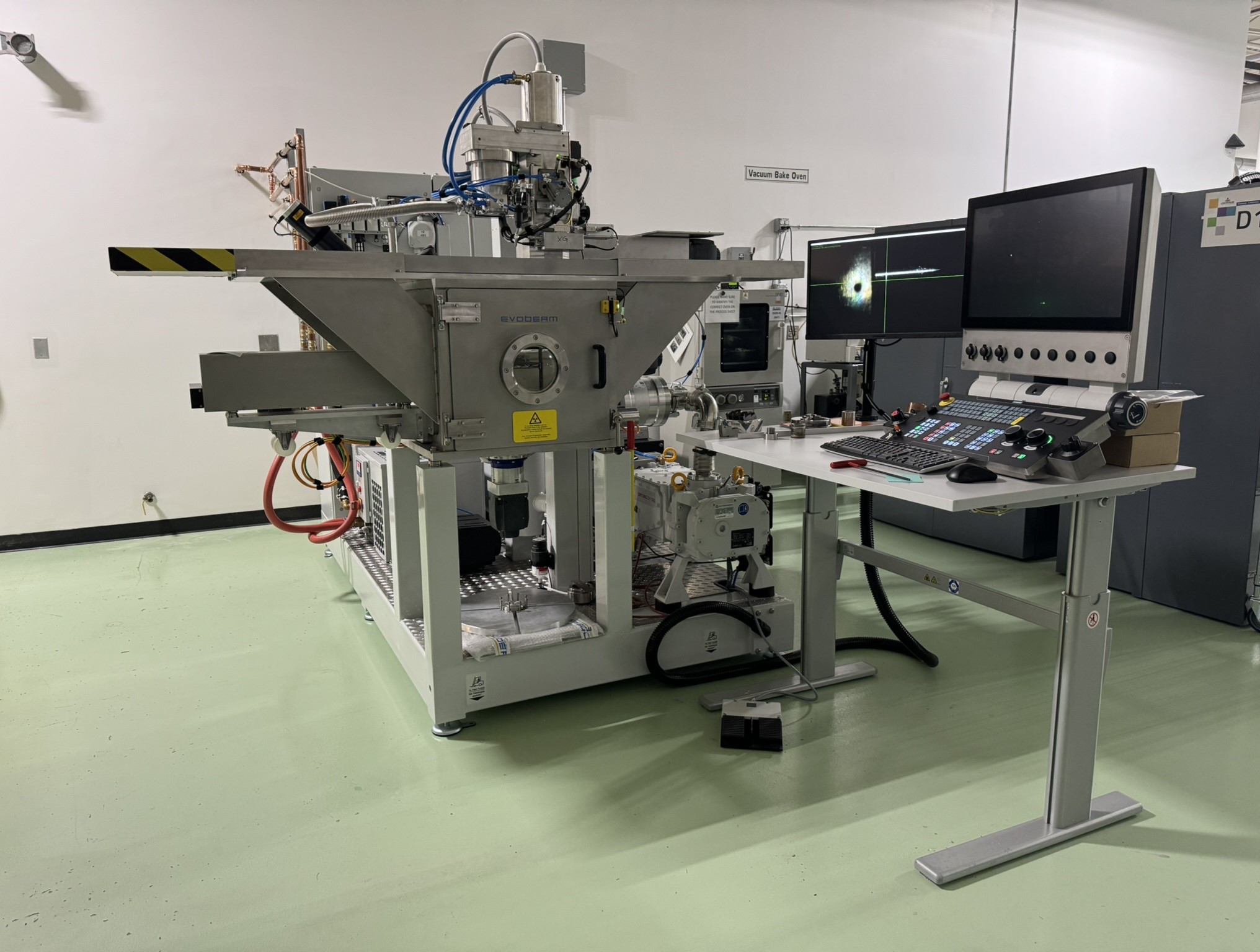
Have Some Questions?
Let us answer them by clicking the button below!
Joining Technologies: AS9100D Approved
What is AS9100D?
AS9100D is a globally recognized quality management system (QMS) standard specifically tailored for the aerospace industry. Developed as an extension of the ISO 9001 standard, AS9100D incorporates additional requirements essential to the aerospace sector. This certification serves as a testament to an organization’s commitment to delivering products and services that meet the stringent standards of the aerospace and defense industries.
Ensuring Product and Process Integrity
At Joining Technologies, our AS9100D certification signifies our dedication to maintaining the highest levels of product and process integrity. This certification provides a structured framework for quality management, emphasizing risk management, traceability, and configuration control. By adhering to these standards, we enhance the reliability and safety of our aerospace components, reinforcing the trust that our clients place in us.
Meeting Industry-Specific Requirements For AS9100D
The aerospace industry demands precision, consistency, and adherence to strict regulatory requirements. AS9100D incorporates these industry-specific requirements, ensuring that our business practices align with the expectations of regulators, customers, and other stakeholders. This not only facilitates compliance but also positions Joining Technologies as a reliable and preferred partner in the aerospace supply chain.
Certified Services:
Competitive Advantage and Market Access
Having this certification is more than a badge of honor; it’s a strategic business move. It opens doors to new opportunities by positioning JoiningTech.com as a trustworthy and capable supplier within the aerospace industry. Many clients and prime contractors require suppliers to hold AS9100D certification, making it a valuable asset that expands our market reach and enhances our competitiveness.
Setting the Standard: Embracing AS9100D Certification at Joining Tech
In summary, AS9100D certification is not just a requirement; it is a strategic investment in the future of our company. It signifies our unwavering commitment to quality, safety, and continuous improvement—core values that define our business. As we continue to push the boundaries of precision engineering, our AS9100D certification serves as a beacon, guiding us toward new heights of excellence in the dynamic and demanding aerospace industry. We’re not just a welding company or a machine shop; we are a partner you can trust for precision, reliability, and innovation.
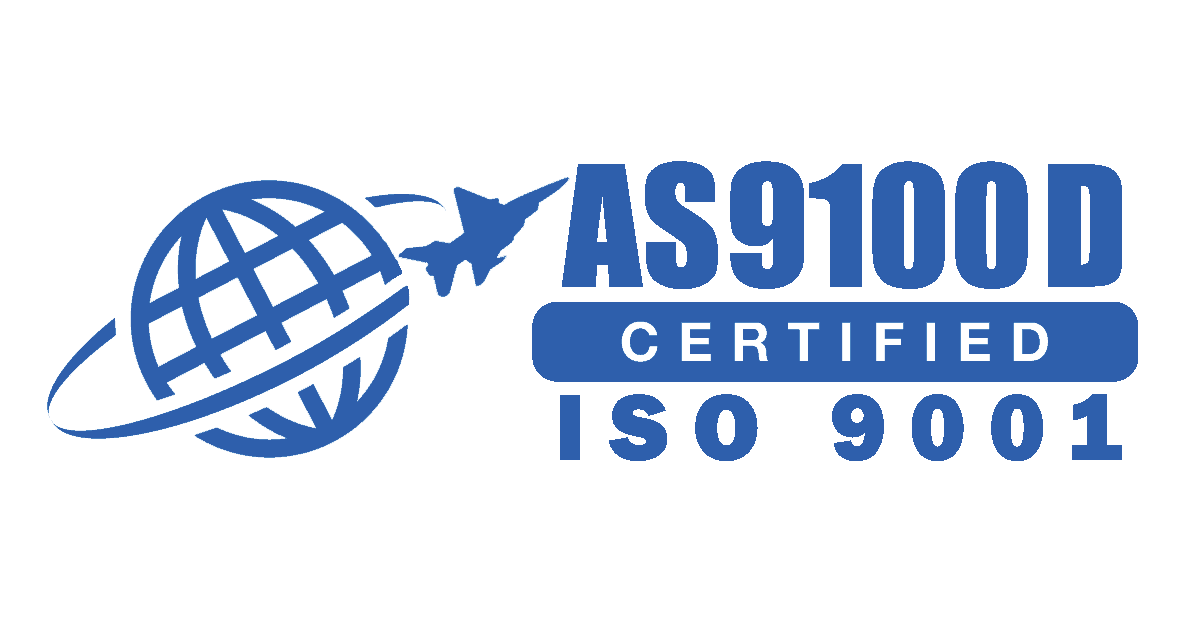
Have Some Questions?
Let us answer them by clicking the button below!
"Revolutionizing Precision Joining: Green Laser Welding"
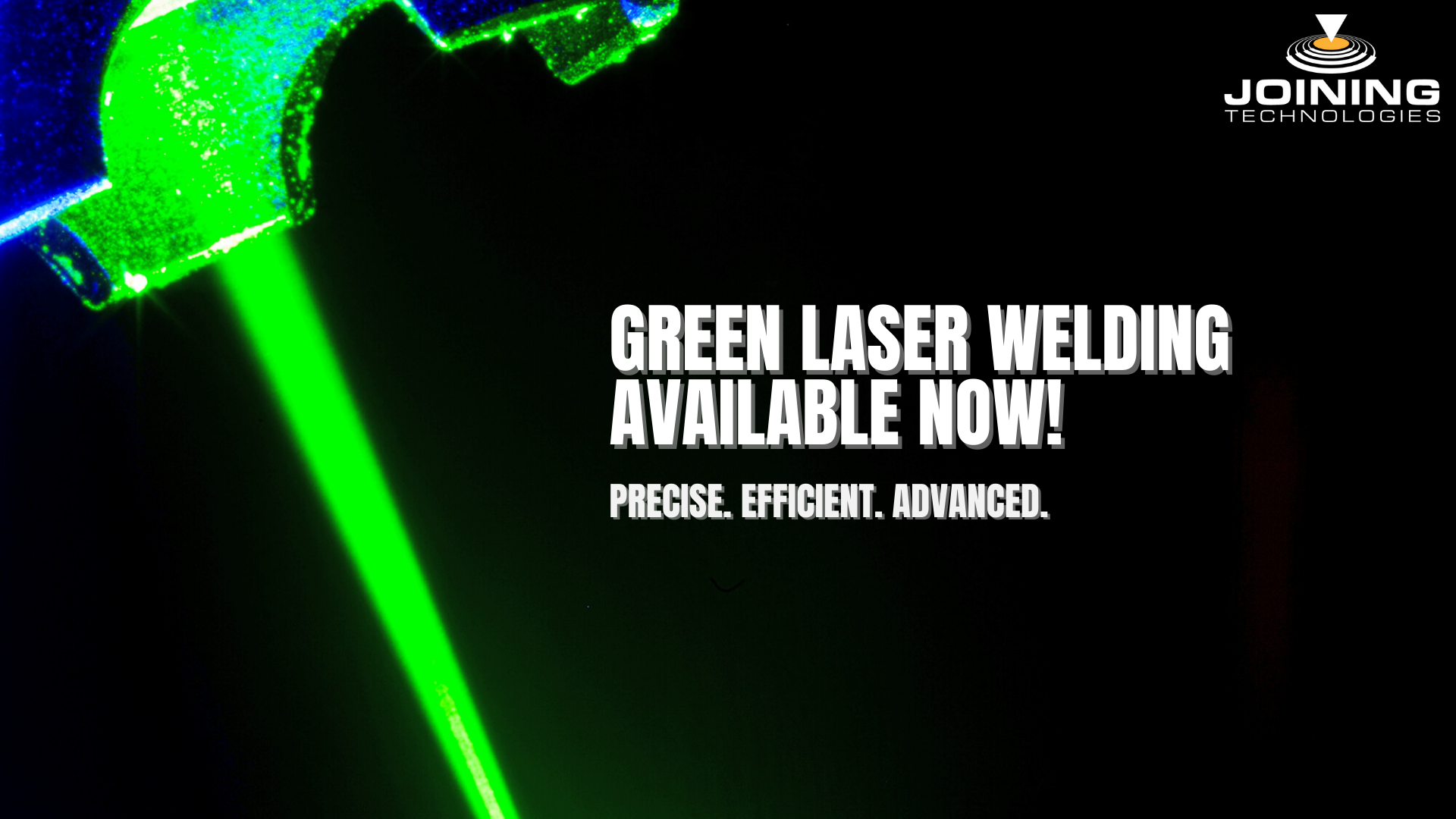
In the ever-evolving landscape of manufacturing and precision engineering, innovation is the key to achieving higher levels of efficiency, precision, and quality. One such groundbreaking advancement in the field of welding technology is the emergence of green laser welding. In this blog post, we will delve into the fascinating world of green laser welding, its advantages, applications, and the future it promises in various industries.
What Is Green Laser Welding?
Green laser welding is an advanced welding technique that utilizes lasers emitting green light with a wavelength of around 532 nanometers. Unlike traditional welding methods, which use infrared or CO2 lasers, it has several unique characteristics that make it a game-changer in many industrial applications.
What Are the Advantages?
- Enhanced Precision – Green laser welding offers exceptional precision and control, making it ideal for applications where accuracy is paramount. The shorter wavelength of green light allows for smaller spot sizes and finer details, resulting in neater welds.
- Reduced Heat Affected Zone (HAZ) – Green lasers generate less heat during the welding process, leading to a smaller HAZ. This minimizes the risk of distortion or damage to sensitive materials, such as electronics or medical devices.
- Improved Absorption – Materials that are traditionally challenging to weld, like copper and gold, absorb green light more efficiently. This widens the range of materials that can be effectively joined using this method.
- Energy Efficiency – Green lasers are more energy-efficient than their counterparts, reducing operational costs and environmental impact.
- Minimal Post-Processing – Thanks to its precision, this process often requires minimal post-processing, saving time and resources in the production cycle.
Green lasers, Green Transportation
While green lasers have solved lots of challenges in recent times, one very popular application is EV batteries. Specifically, connectors and busbars. Copper and aluminum are sought after in battery assemblies for their conductivity, but again, they are also among the most reflective metals, and challenging to weld. This is just one of the challenges to overcome as automobile OEM’s race to build a higher performing EV battery.
Here at Joining Technologies, that challenge is an opportunity to help automotive manufacturers build a better battery and meet ever-growing product demand in the most efficient way possible.
A green laser excels at welding reflective materials, doing so efficiently, without creating spatter, and without making contact. Controlled heat affected zones prevent the interior contents of the battery from being disturbed.
The reliable results achieved using a green laser translates to more batteries produced in a shorter window. Manufacturers meet demand while decreasing costs. Further, reduced manufacturing costs means more competitive price tags. Thanks to the higher quality of the welds, and the ability to work with conductive materials, batteries are much more efficient and hold a charge for an extended amount of time. Welding innovations like this are allowing electric cars to go greater distances before needing a recharge.
Other Applications & Industries
The versatility of this process has led to its adoption in various industries:
- Electronics – This method is used to assemble delicate electronic components with precision and minimal heat impact.
- Medical Devices – Medical devices, such as pacemakers and catheters, benefit from the precision and cleanliness of this method.
- Aerospace – In the aerospace industry, green laser welding is employed to create lightweight, strong joints in aircraft components.
What Does the Future Look Like?
As technology continues to advance, we can expect this process to continue to play an increasingly pivotal role in various industries. Research and development efforts are ongoing to expand the range of materials that can be effectively welded using this technique. Additionally, automation and robotics are being integrated with green laser welding systems to enhance productivity and consistency.
In conclusion, this new method represents a significant leap forward in precision joining technology. Its ability to provide unparalleled precision, reduce heat-affected zones, and broaden the range of weldable materials makes it an invaluable tool in the manufacturing world. As this technology continues to evolve, its impact on industries across the board is set to grow, reshaping the way we approach precision welding.
If you’d like to learn if this process is right for your job, ask an expert or request a quote now!
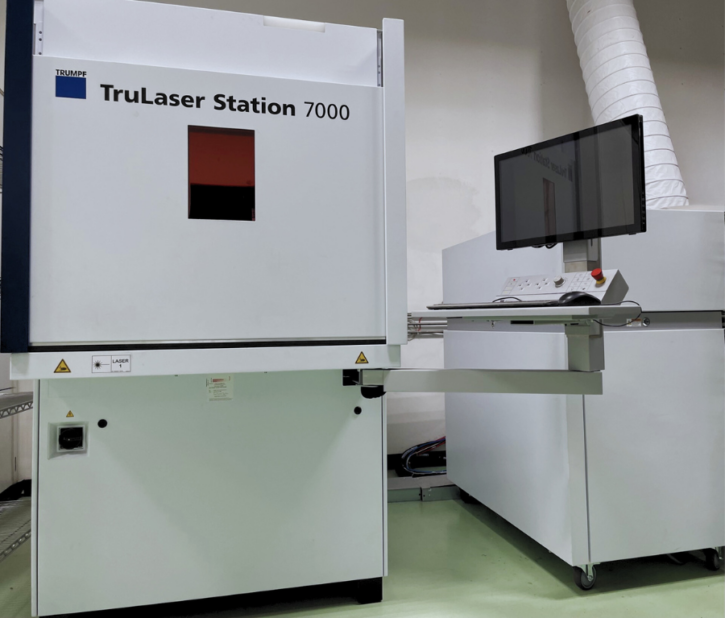
Have Some Questions?
Let us answer them by clicking the button below!